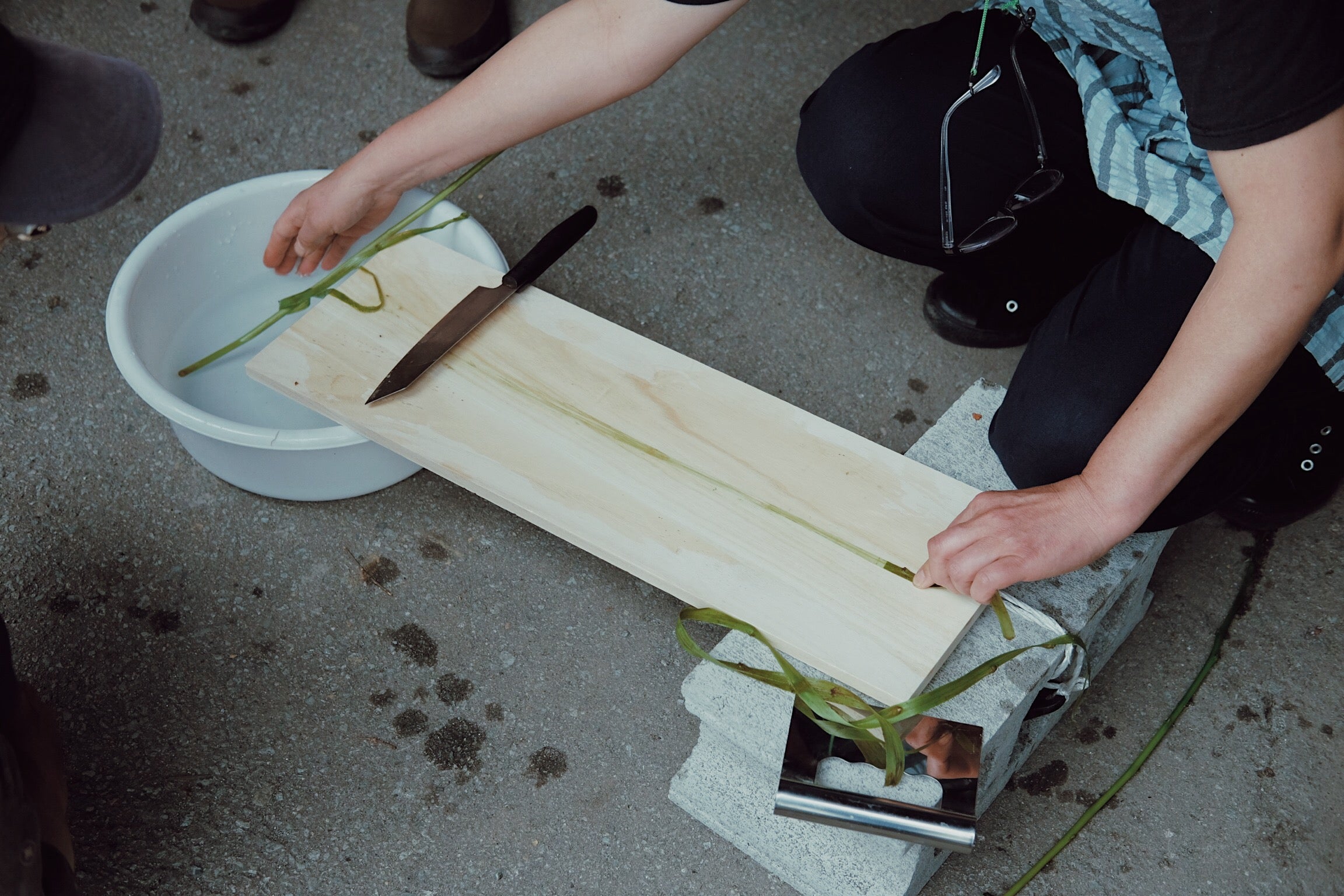
Locally-rooted traditional textile making employed sophisticated techniques to rival those of today. YUIKOUBOU +Yoshikatsu seeks to recover and teach these techniques, to be passed on for generations to come.
YUIKOUBOU + Yoshikatsu designs textiles and conducts fieldwork and research in the Tohoku region on ancient artisanal techniques that have been handed down from generation to generation.
Their work encompasses traditional silk harvesting, native plant fiber harvesting, spinning, dyeing, and weaving. They also facilitate workshops in which they teach textile making from start to finish, beginning with harvesting the natural materials such as silk cocoons and plants, to processing them into fibers, dying the threads, and weaving textiles with them.
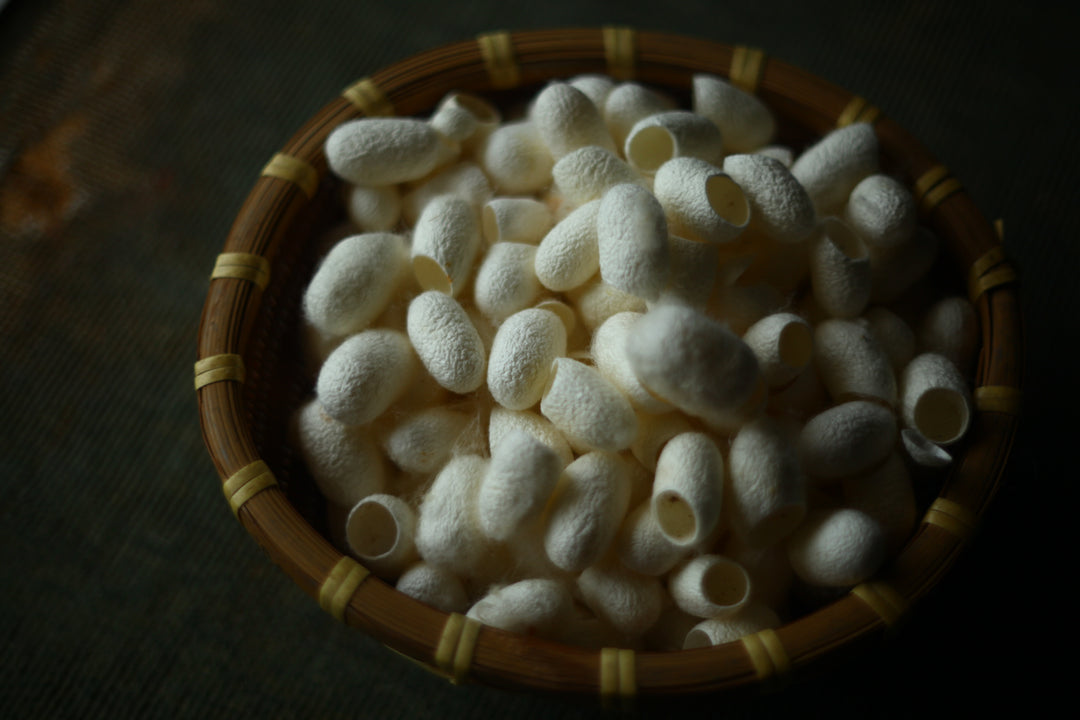
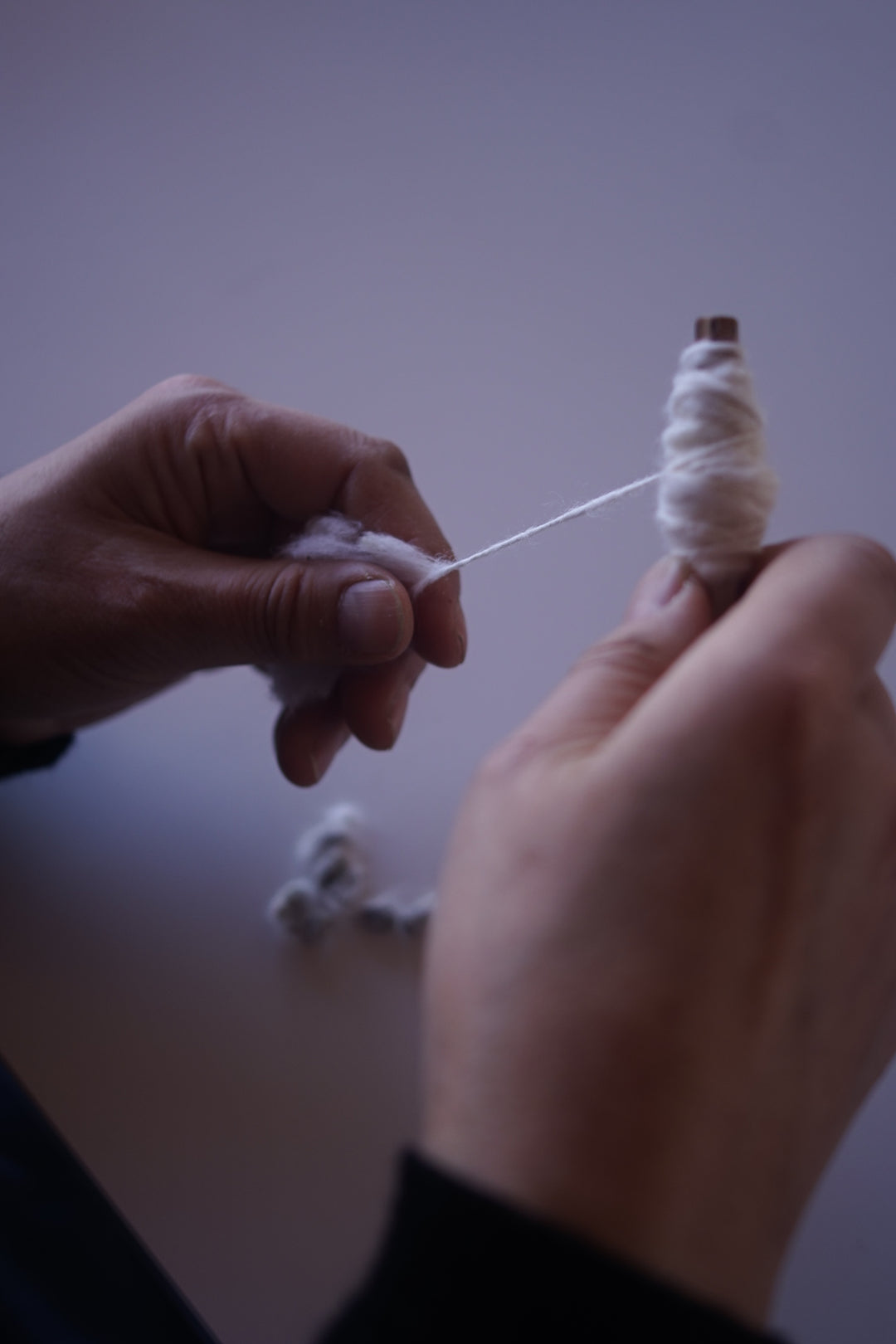
China, India, and Japan have all developed their own silk production techniques. Japanese silk harvesting, fiber sorting, reeling, twisting and dying methods have been around since at least 552 AD.
Although silk is known as a luxurious and valuable commodity traded around the world, Japanese silk was produced for domestic use for most of its history until the 1870’s. As a result, many local techniques were developed over more than 1000 years.
Later, with the opening of Japan to the rest of the world, silk was rapidly modernized for export, and many farmers began sericulture, or silk farming, on the side. Most cocoons were shipped to silk mills to be turned into raw silk, but cocoons that could not be shipped due to soiling or other reasons were turned into thread and woven into household fabrics. The unique regional weaving techniques that developed remain in many parts of Japan and can be seen in local kimono and other textiles used by silk farmers.
YUIKOUBOU + Yoshikatsu uses silk cocoons from regions of Miyagi where sericulture has flourished since the Edo Period. Sericulture evolved as a side-hustle for farmers in the region, who became skilled not only at raising cocoons, but also at spinning and weaving. There are more than a dozen silkworm farms in the villages along the Abukuma River which runs through Miyagi and Fukushima, where silk culture is still woven into the local identity. YUIKOUBOU is helping to contribute to and continue this culture through its various activities.
Aoso is the local dialect for ramie, also known as karamushi. This shrub, belonging to the nettle family, is widely distributed in East Asia and also grows wild in Japan. It was first used in Japan as a cloth fiber in the Jomon period (1400 BC to 1000 BC). When made into cloth, it has a hemp-like quality.
YUIKOUBOU + Yoshikatsu uses ramie from Oe in Yamagata Prefecture, where their studio is located. Oe was a thriving ramie producing region during the Edo Period, and in recent years its tradition has been revived by the local people.
Oe ramie plants are short and delicate, and their fibers are transparent and crisp. Fibers are refined by hand in a skilled process called "ohiki.”
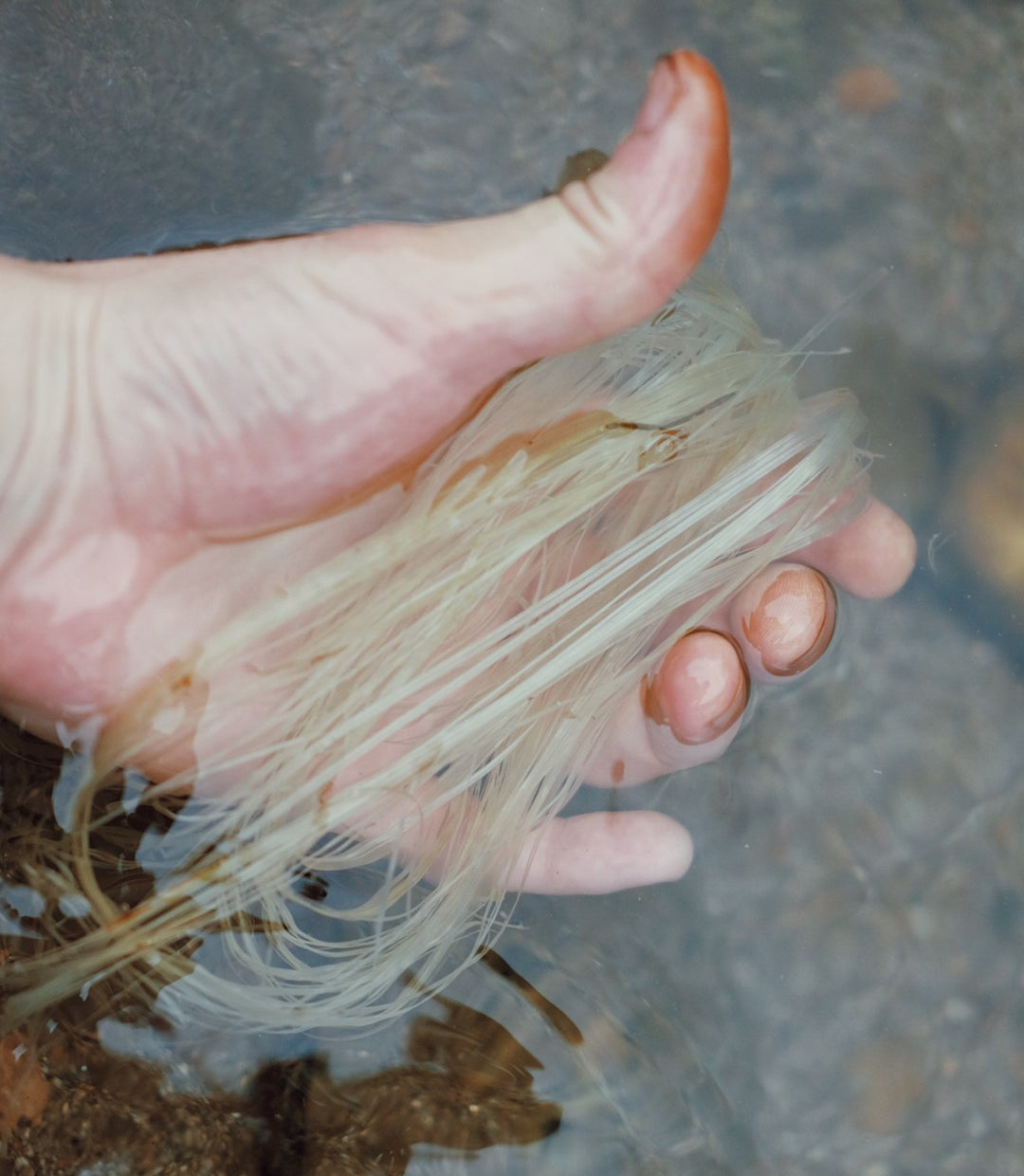
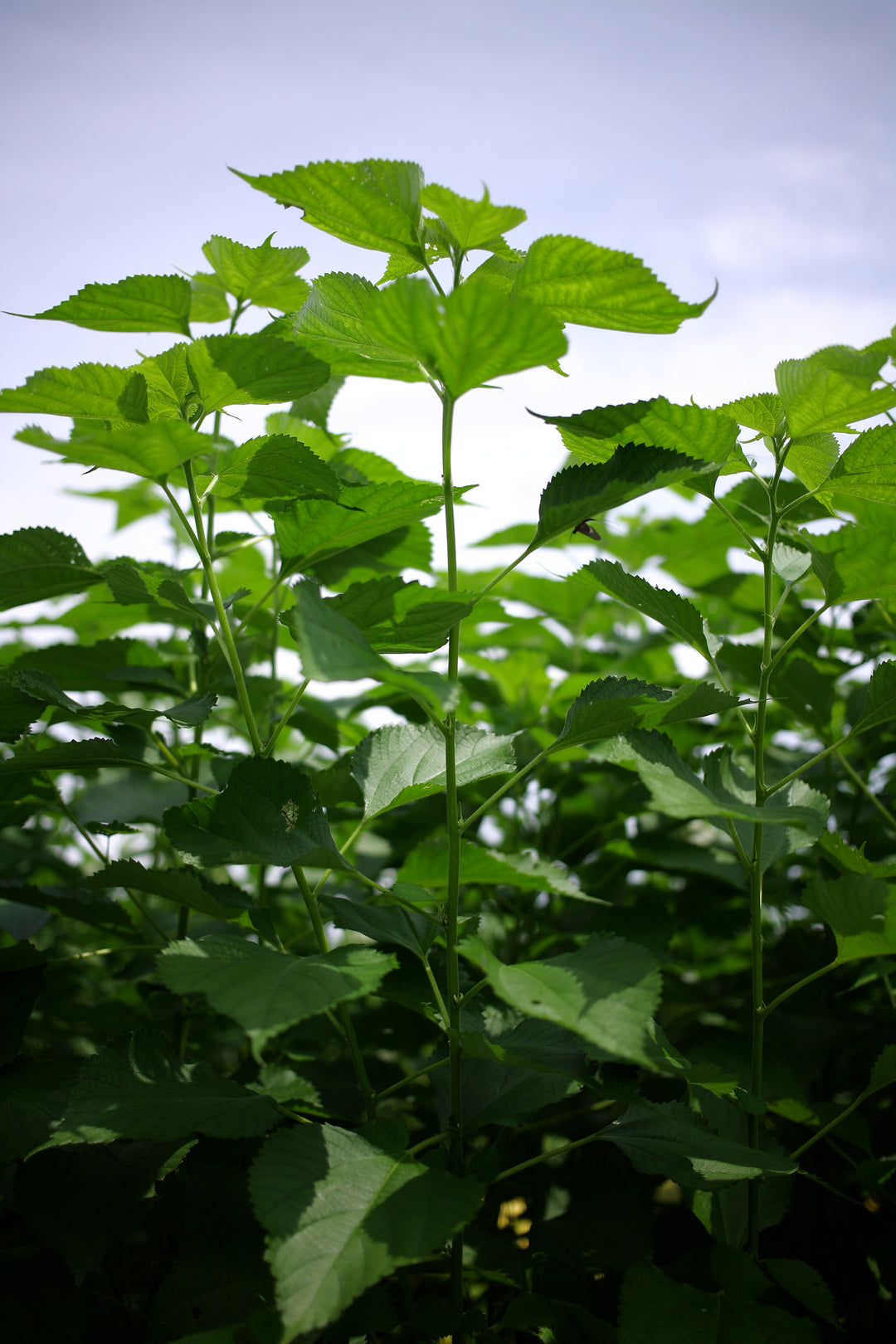
YUIKOUBOU + Yoshikatsu almost exclusively uses plant-based dyes, using plant and indigo dyeing techniques that have been practiced since the Nara Period (710 - 794). Plant-based dyes, which are developed for dyeing silk, are made with both gardened and wild plants. Indigo dyeing, which is developed for dyeing plant fibers, is done through a process of fermenting indigo plants into a dye which becomes a vibrant indigo color when oxidized.
