Washi is a material that has been an inseparable part of Japanese life for centuries. Not only is it used for writing and painting, but also for construction, lanterns, toys, umbrellas, fans, ceremonial objects, and more. Various washi paper processing methods have been developed by skilled craftspeople across history to suit different uses and needs.
The history of Inshu washi can be traced back 1300 years, when it was managed by the Tottori Clan. It is produced in the Aoya and Saji areas of eastern Tottori Prefecture, historically known as Inaba. During the Meiji period, the demand for washi for government registers and construction materials increased, and by the late 1800’s there were as many as 100 workshops in operation.
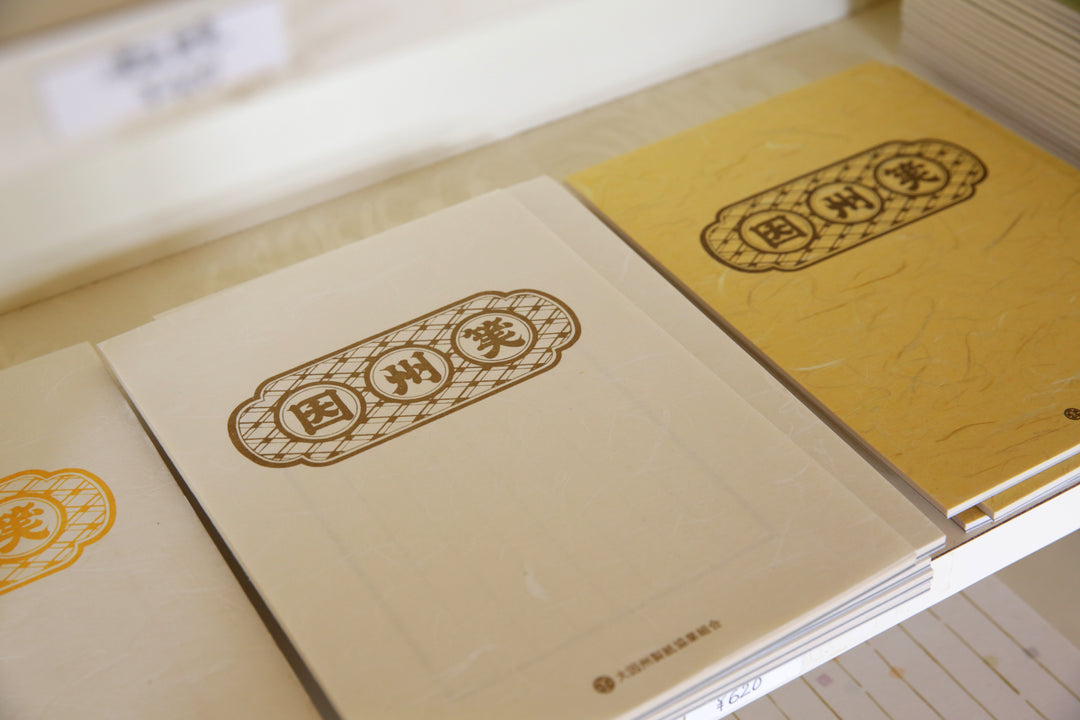
Each producer of Inshu washi developed their washi differently, with some artisans adhering strictly to handmade techniques only, and others introducing technology to increase their output.
During the post-war period with the import of western-style paper, demand for washi decreased, but even so, washi artisans continued to preserve and pass down their traditional techniques, so many different kinds of washi remain.
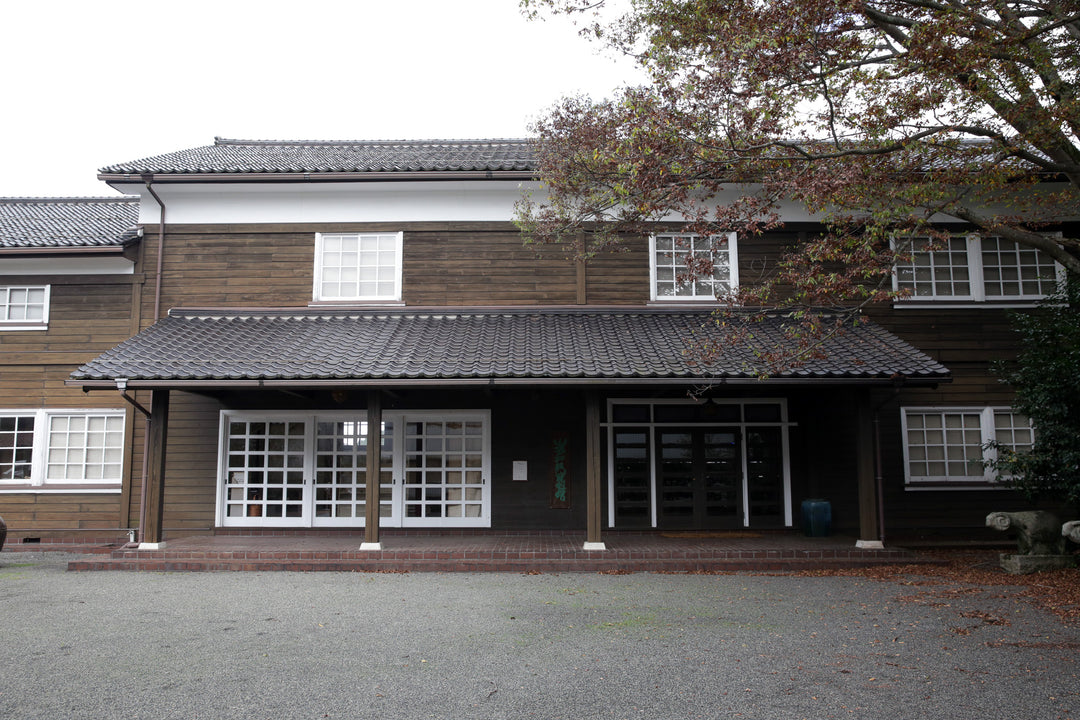
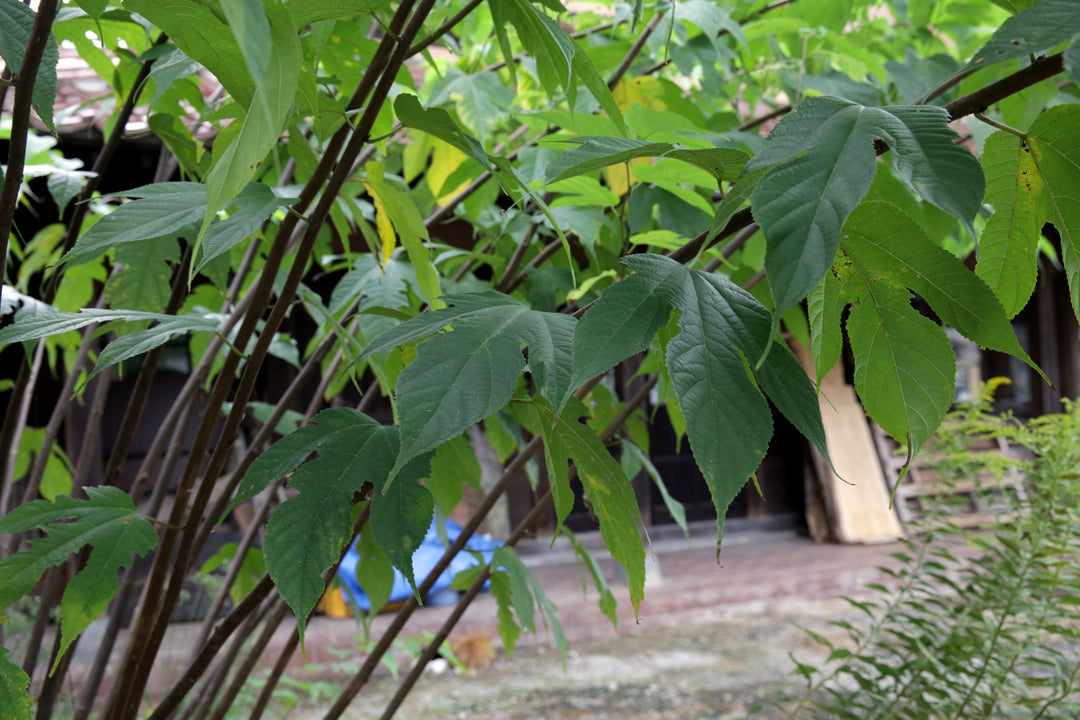
There is a well known saying, “Inshu brushes never run out,” which refers to the smooth and easy way that a calligraphy brush runs along the fine-texture of Inshu washi, which helps the ink last for several strokes. Although demand for washi has decreased in modern days, Inshu washi accounts for more than sixty percent of calligraphy washi (gasen-shi) used in Japan, and many artists and calligraphers order custom Inshu washi to work with.